Rainier delivers high levels of customer satisfaction by producing superior quality products and continually improving our Quality Management System
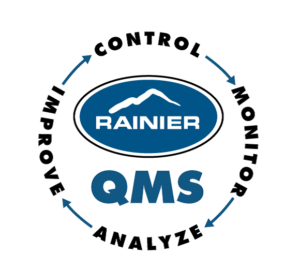
It is a core principle at Rainier to build great products. As a growing organization, we found many of our processes and past success were dependent on tribal knowledge and “good, old-fashioned craftsmanship.” With new people coming in faster than our tribal system could absorb, we recognized a need for a more systematic approach to quality control in training our work force to build product correctly the first time with proper fit, finish and functionality.
In 2007, we launched our Quality Management System (QMS). We are proud to be able to say that both our state-of-the-art manufacturing facilities have an in-depth Quality Management System certified to conform to ISO 9001:2015. The work of achieving lasting quality improvements is an everyday activity at Rainier. QMS gives us the framework to control, monitor, analyze, and improve. The bottom line is that a good quality system can only be achieved through the hard work of the people supporting it – QMS is now ingrained into Rainier’s culture. We are fortunate to have a team that recognizes the need for high-quality products and continuous improvement.
ISO certification requires an independent auditor and there were many to choose from. We selected TUV Rhineland, a company well known in our industry (us.tuv.com). TUV Rhineland is an expensive audit alternative, but we chose use knowing their audits will be stringent and meaningful. We find our annual audit to be rigorous but helpful –auditors are consistently interested in our success and provide valuable feedback to allow us continuous improvement in our quality and our customer experiences. QMS, coupled with a committed team, allows us to improve our manufacturing processes.
Click the links to view our QMS Certificate, Policy, and Manual with Scope.